Main Components Material
Item | Name | Materials |
1 | Valve body | Ductile iron QT450-10 |
2 | Valve cover | Dductile iron QT450-10 |
3 | Floating ball | SS304/ABS |
4 | Sealing ring | NBR/Alloy Steel,EPDM Alloy steel |
5 | Dust screen | SS304 |
6 | Explosion proof flow limited check valvle(optional) | Ductile iron QT450-10/Bronze |
7 | Back-flow preventer(optional) | Ductile iron QT450-10 |
Detailed Size of Main Parts
Nominal Diameter | Nominal pressure | Size(mm) | |||
DN | PN | L | H | D | W |
50 | 10 | 150 | 248 | 165 | 162 |
16 | 150 | 248 | 165 | 162 | |
25 | 150 | 248 | 165 | 162 | |
40 | 150 | 248 | 165 | 162 | |
80 | 10 | 180 | 375 | 200 | 215 |
16 | 180 | 375 | 200 | 215 | |
25 | 180 | 375 | 200 | 215 | |
40 | 180 | 375 | 200 | 215 | |
100 | 10 | 255 | 452 | 220 | 276 |
16 | 255 | 452 | 220 | 276 | |
25 | 255 | 452 | 235 | 276 | |
40 | 255 | 452 | 235 | 276 | |
150 | 10 | 295 | 592 | 285 | 385 |
16 | 295 | 592 | 285 | 385 | |
25 | 295 | 592 | 300 | 385 | |
40 | 295 | 592 | 300 | 385 | |
200 | 10 | 335 | 680 | 340 | 478 |
16 | 335 | 680 | 340 | 478 |
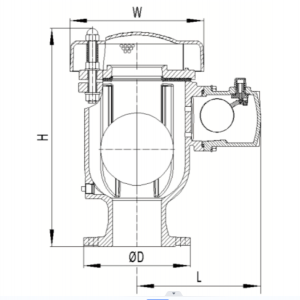
Product Features Advantages
Efficient Air Exhaust and Intake: When the pipeline system starts to transport liquid, the Combined Type Air Vent Valve can quickly and in large quantities expel the accumulated air in the pipeline, avoiding air resistance and ensuring smooth liquid transportation. When the pipeline is emptied, it can promptly intake air to balance the pressure inside and outside the pipeline, preventing the pipeline from deforming due to negative pressure. This efficient air exhaust and intake capability greatly improves the operating efficiency of the pipeline system and reduces the time loss during the startup and emptying processes.
Prevention of Water Hammer and Cavitation: The water hammer phenomenon can generate instantaneous high pressure, severely impacting the pipeline and equipment, while cavitation will erode the inner wall of the pipeline. Both can significantly shorten the service life of the pipeline system. The Combined Type Air Vent Valve effectively buffers the pressure fluctuations by precisely controlling the intake and exhaust of air, greatly reducing the water hammer effect. At the same time, it reduces the formation and bursting of bubbles in the liquid, thus significantly alleviating the cavitation phenomenon. It comprehensively protects the pipeline system and reduces the frequency and cost of maintenance.
Combination of Multiple Functions: It integrates multiple functions. There is no need to install multiple valves with different functions in the pipeline system to separately achieve operations such as air exhaust and intake. This characteristic of combining multiple functions not only simplifies the design and installation process of the pipeline system, reduces the number of valves, but also lowers the probability of system failures and improves the overall stability and maintainability.
Compact Structure: This valve has a delicate design and a small size, occupying very little space. Whether in the renovation projects of existing pipeline systems with limited space or in the newly built pipeline layouts with high requirements for space utilization, it can be easily installed and flexibly adapted to various complex installation environments, bringing great convenience to engineering design and construction.
High Reliability: High-quality and durable materials are selected for manufacturing the Combined Type Air Vent Valve, which has excellent wear resistance and can withstand the continuous erosion of the fluid in the pipeline. Meanwhile, it has good corrosion resistance and can deal with various corrosive media. This enables it to operate stably for a long time under harsh working conditions such as high temperature, high pressure, and strong corrosion, ensuring the continuous normal operation of the pipeline system, and greatly reducing the maintenance cost and the risk of production interruption.